Why do PCB Circuit Boards Need to be Tested?
2020-09-16
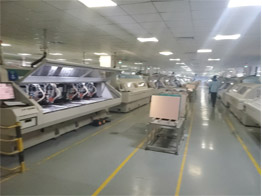
As a PCB Assembly Manufacturer, share with you. For people studying electronics, it is natural to set up test points on the circuit board, but for people studying machinery, what are the test points?
Basically, the purpose of setting test points is to test whether the components on the circuit board meet the specifications and solderability. For example, if you want to check whether there is any problem with the resistance on a circuit board, the easiest way is to measure with a multimeter. You can know it by measuring both ends.
However, in a mass production factory, there is no way for you to use an electricity meter to slowly measure whether each resistance, capacitance, inductance, and even the circuit of each IC on each board is correct, so there is the so-called ICT automation. The emergence of the test machine uses multiple probes (generally called "Bed-Of-Nails" fixtures) to contact all the parts on the board that need to be measured at the same time, and then the sequence is controlled by the program. The main and side-by-side methods are used to measure the characteristics of these electronic parts sequentially. Usually, it only takes about 1 to 2 minutes to test all the parts of the general board. It depends on the number of parts on the circuit board. The more parts time The longer.
But if these probes directly touch the electronic parts on the board or its solder feet, it is likely to crush some electronic parts, which will be counterproductive. So smart engineers invented "test points" at both ends of the parts. A pair of small circular dots are additionally led out, and there is no solder mask on them, so that the test probe can touch these small dots without directly contacting the electronic parts to be measured.
In the early days of DIP on the circuit board, the solder feet of the parts were indeed used as test points, because the solder feet of the traditional parts were strong enough not to be afraid of needle sticks, but there were often errors of poor probe contact. Judgment occurs, because after general electronic parts undergo wave soldering or SMT tin, a residual film of solder paste flux is usually formed on the surface of the solder. This film has very high impedance and often causes probes. The contact was poor, so test operators on the production line were often seen at that time, often holding an air spray gun to blow desperately, or using alcohol to wipe these places that needed to be tested.
Our company also has Prototype PCB on sale, welcome to contact us.